Fine Grinding & Flat Honing
A High-Speed Lapping Process
Fine grinding and flat honing both describe the same revolutionary, low-cost surface finishing process. Fine grinding / flat honing is a high-speed lapping process capable of achieving high precision finishes at very reasonable costs.
The fine grinding / flat honing process was first developed by leading European machine producers approximately twenty years ago. The process quickly became popular in Europe and was introduced to the United States, where fine grinding / flat honing has become a preferred technique for finishing high-precision parts at a very low cost.
While the fine grinding / flat honing process is considered either high-speed lapping or high precision grinding, it in fact combines the advantages of both traditional lapping and grinding techniques. Fine grinding / flat honing uses fixed abrasive wheels which allow for relatively rapid stock removal and eliminate the time-consuming cleanup associated with free abrasive processes. The fine grinding / flat honing process also uses advanced machine controls to achieve precision levels nearly equivalent to traditional flat lapping.
Ideal for All Types of Components
Fine grinding / flat honing is ideal for all types of metals, ceramics, plastics, glass, carbon, hard-anodized surfaces, and other materials. Components of most sizes and shapes can be quickly and easily processed, including rings, seals, heat sinks, gears, bearings, rollers, slitter knives, cutting tools, and others. These components are used in a variety of devices including precision pistons, automotive sensors, valves, gear pumps, rotary pumps, faucets, computers, telecommunication devices, and virtually any product with a sealing surface.
Features & Advantages
- Fixed Abrasives – Fixed abrasives eliminate the time-consuming cleanup associated with free abrasive processes such as conventional lapping.
- Advanced Machine Controls – Advanced machine controls combine the high-speed stock removal rates of grinding with the slower, more precise finishing of conventional lapping.
- Automation – High-speed handling of parts is achieved through automated part loading and unloading.
- Low Cost – High-speed lapping is up to ten times faster than conventional lapping. This yields savings of up to 40%!
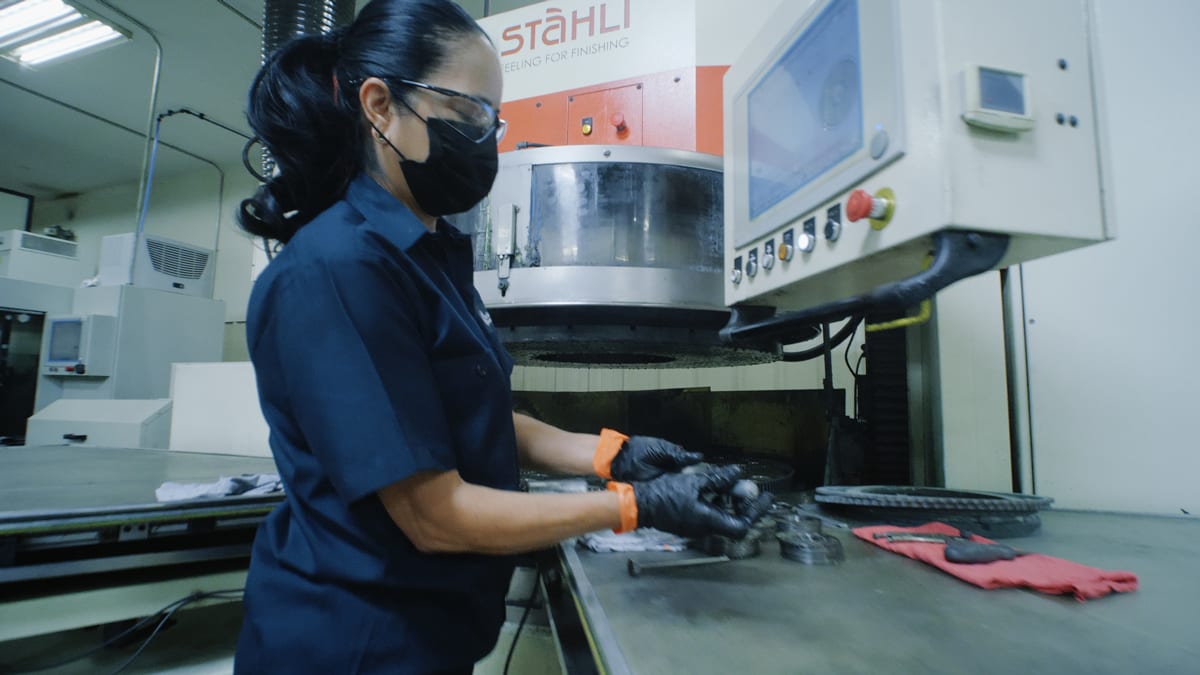